Polyester disperse printing fabric is a type of fabric that is printed using the disperse dyeing process, which involves using disperse dyes that are specifically designed for polyester fibers. Here are the general production steps involved in creating polyester disperse printing fabric:
Fabric Preparation: The first step is to prepare the polyester fabric for printing. This involves processes such as desizing, scouring, and bleaching to remove any impurities, sizing agents, or natural oils present in the fabric. The fabric is then thoroughly washed and dried.
Design Creation: The next step is the creation of the design that will be printed on the fabric. This can be done through various methods, such as hand-drawing, digital design, or screen printing. The design is typically created in a repeat pattern, which allows it to be seamlessly repeated across the fabric.
Color Preparation: Disperse dyes are available in a wide range of colors. The desired colors for the design are selected, and the disperse dyes are prepared accordingly. The dyes are usually in powder or liquid form and need to be dissolved or dispersed in a suitable medium or carrier.
Printing Process: The printing process involves transferring the design onto the polyester fabric using the disperse dyes. There are different methods for printing, including screen printing, rotary printing, or digital printing. Each method has its own set of requirements and equipment.
Screen Printing: In screen printing, a screen with a fine mesh is prepared, and the design is transferred onto the screen using a light-sensitive emulsion or a stencil. The dye paste or ink is applied onto the screen, and a squeegee is used to force the dye through the mesh onto the fabric.
Rotary Printing: Rotary printing involves the use of cylindrical screens with perforations to create the design. The dye paste or ink is fed into the perforations, and as the fabric moves under the screens, the dye is forced through the perforations onto the fabric.
Digital Printing: Digital printing utilizes computer-controlled printers to directly apply the disperse dyes onto the fabric. The design is digitally processed and then printed onto the fabric using specialized inkjet heads.
Fixation: After the printing is done, the fabric needs to go through a fixation process to ensure the color fastness of the disperse dyes. Fixation can be achieved through heat setting, which involves passing the printed fabric through a heated chamber or using a hot press. The heat causes the disperse dyes to sublimate and bond with the polyester fibers, resulting in a permanent coloration.
Washing and Finishing: Once the fixation process is complete, the fabric is washed to remove any excess dye or printing auxiliaries. This is followed by finishing processes such as softening, drying, and any other required treatments to enhance the fabric's appearance and properties.
Quality Control: Throughout the production process, quality control measures are implemented to ensure that the fabric meets the desired standards. This involves checking for color accuracy, design alignment, print clarity, and overall fabric quality.
Besides,Polyester disperse printing fabric offers several advantages compared to other types of printing fabrics. Here are some of the key advantages:
Excellent Color Fastness: Polyester disperse printing fabric exhibits excellent color fastness properties, meaning that the colors remain vibrant and do not fade easily over time. Disperse dyes have a strong affinity for polyester fibers, resulting in a durable and long-lasting coloration.
Wide Range of Colors: Disperse dyes offer a wide range of color options, allowing for vibrant and intricate designs to be printed on the fabric. These dyes can achieve intense and saturated colors, giving designers and manufacturers greater creative freedom.
Good Print Definition: Polyester disperse printing fabric provides good print definition, meaning that the printed designs are sharp, clear, and precise. This allows for intricate patterns, fine details, and complex designs to be accurately reproduced on the fabric.
Versatility: Polyester disperse printing fabric is versatile and can be used for various applications, including apparel, home textiles, upholstery, and more. It can be printed with different designs and patterns to suit different styles and preferences.
Durability: Polyester fibers are known for their strength and durability, and this translates into polyester disperse printing fabric. The fabric is resistant to wear, tear, and wrinkling, making it suitable for garments and textiles that require long-lasting performance.
Easy Care: Polyester disperse printing fabric is relatively easy to care for. It is wrinkle-resistant and has low shrinkage properties, allowing it to maintain its shape and appearance after washing. It also dries quickly, reducing the need for extensive drying time.
Cost-Effective: Polyester is a cost-effective fabric compared to natural fibers such as silk or cotton. Polyester disperse printing fabric offers a balance between quality and affordability, making it a popular choice for mass production and commercial applications.
Resistance to Moisture and Chemicals: Polyester fibers have inherent moisture-wicking properties, meaning that they are resistant to moisture absorption and can dry quickly. Additionally, polyester disperse printing fabric has good resistance to chemicals, making it suitable for environments where exposure to various substances is likely.
Environmental Considerations: Polyester disperse printing fabric can be produced using recycled polyester fibers, contributing to sustainability efforts. Additionally, the printing process for polyester disperse fabric typically requires less water and energy compared to some other printing methods.
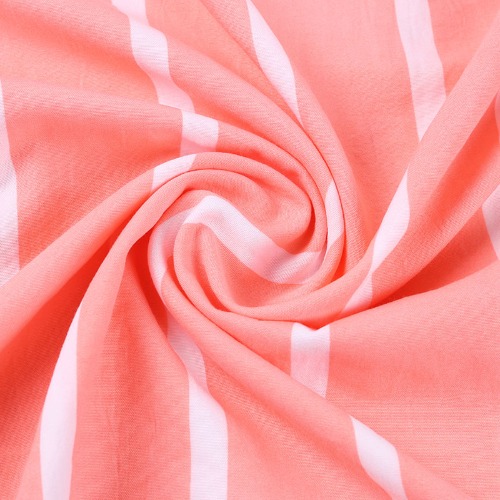
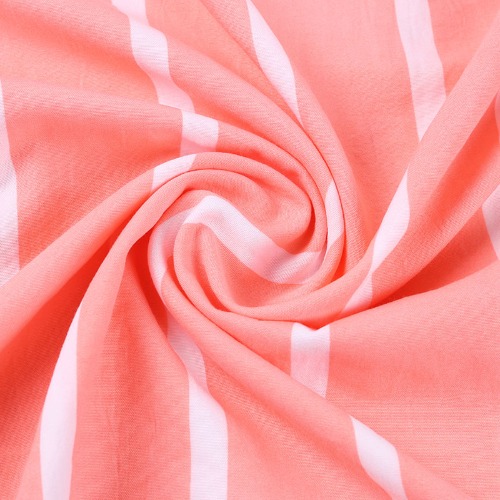